- Joined
- Dec 19, 2016
- Messages
- 2,548
With Fall and Winter setting in, I decided that i wanted to build another of the DeHass Chicopee single shots. Ive been wanting a 22 Hornet so I think thats what this on will be. I ordered the steel a couple of weeks ago and started cutting things out this weekend. The last one took a little over 3 years to build. During that time i had to acquire some tools, tooling, and a whole lot of knowledge. I initially thought about building one of the other actions he has in the book "Mr. Single Shots Book of Rifle Plan", after a tremendous amount of inward reflection i decided that I didnt do too great on the first Chicopee and that i should focus on producing a better one of those before trying something more advanced. More of a crawl, crawl some more, walk, walk some more, RUN philosophy 
The thing about this rifle plan is that is a 1:1 template for the drawings in the book. You print the drawings out and use them as a pattern for your cuts and shaping. This way may be upsetting to some real Machinist since there are not a lot of dimensions given in these drawings, but that is how DeHass wanted it. You dont have to be a master machinist to make it.
Lets start with the raw Cold rolled stock R-L: 1/4 x 2, 3/16 x 1 1/2, 1/8 x 1, and 1 1/8 x 1 all are 12 inches long.
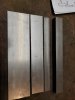
The first thing was to rough out some parts on the bandsaw. I started with the action side plates. Once i hade them roughed out, i drilled both sides for locating pins and pinned them together. I performed all the machining to them while they are pinned so that both half would be identical. I did the swinging block the same way.
Action Side plates top, Swinging block bottom.
Because this is a Swinging block design, the block travels in an arc of a circle. The back of the swinging block needs to be radiused. The pin location on the front (narrow) end of the block is the pivot pin location. The plans do call for a measurement of 3.82ish inches from the pivot to all points on the radiused end of the block. To get the radius that i needed, i secured a piece of angle iron in the mill vise and drilled/reamed a hole for the temporary pivot pin to be in. I placed a grinding wheel in my mill head and started grinding the radius.
Thats all i have for now. There should be more coming, i just have to figure out how to sneak out of the house in the evenings.
The thing about this rifle plan is that is a 1:1 template for the drawings in the book. You print the drawings out and use them as a pattern for your cuts and shaping. This way may be upsetting to some real Machinist since there are not a lot of dimensions given in these drawings, but that is how DeHass wanted it. You dont have to be a master machinist to make it.
Lets start with the raw Cold rolled stock R-L: 1/4 x 2, 3/16 x 1 1/2, 1/8 x 1, and 1 1/8 x 1 all are 12 inches long.
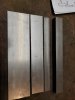
The first thing was to rough out some parts on the bandsaw. I started with the action side plates. Once i hade them roughed out, i drilled both sides for locating pins and pinned them together. I performed all the machining to them while they are pinned so that both half would be identical. I did the swinging block the same way.
Action Side plates top, Swinging block bottom.
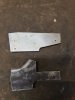
Because this is a Swinging block design, the block travels in an arc of a circle. The back of the swinging block needs to be radiused. The pin location on the front (narrow) end of the block is the pivot pin location. The plans do call for a measurement of 3.82ish inches from the pivot to all points on the radiused end of the block. To get the radius that i needed, i secured a piece of angle iron in the mill vise and drilled/reamed a hole for the temporary pivot pin to be in. I placed a grinding wheel in my mill head and started grinding the radius.
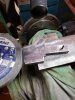
Thats all i have for now. There should be more coming, i just have to figure out how to sneak out of the house in the evenings.